Until then I only had done full tang knives where two handle scales are glued to the sides of the blade. I had seen some videos of my favorite knifemakers how they make knives where the tang is not visible and the wood of the handle goes all around the steel that reaches inside the grip.
Both ways have their pros and cons. I think the full tang is more robust if the knife is used with lots of force. Your hand is always around the full width of the blade and the stress the handle scales are exposed to is less than on hidden tang knives. The hidden tang knives give you completely other options to design the knife. For example you could better fit a guard. And when the full tang knife ages and the wood moves the scales might form a gap between the wood and the tang – something that cannot happen when the wood is all around the tang.
Beside all pros and cons I wanted to try new techniques and designs and I also wanted to experiment with a guard. So I designed a Bowie knife on my computer. I used the blade design of the knife I made for my brother. I just shortened the blade a bit because I would use the 3,2 mm 1.2003 steel I had enough of in my workshop. As the steel was much thinner than on “Mike” I did not want a blade that long.
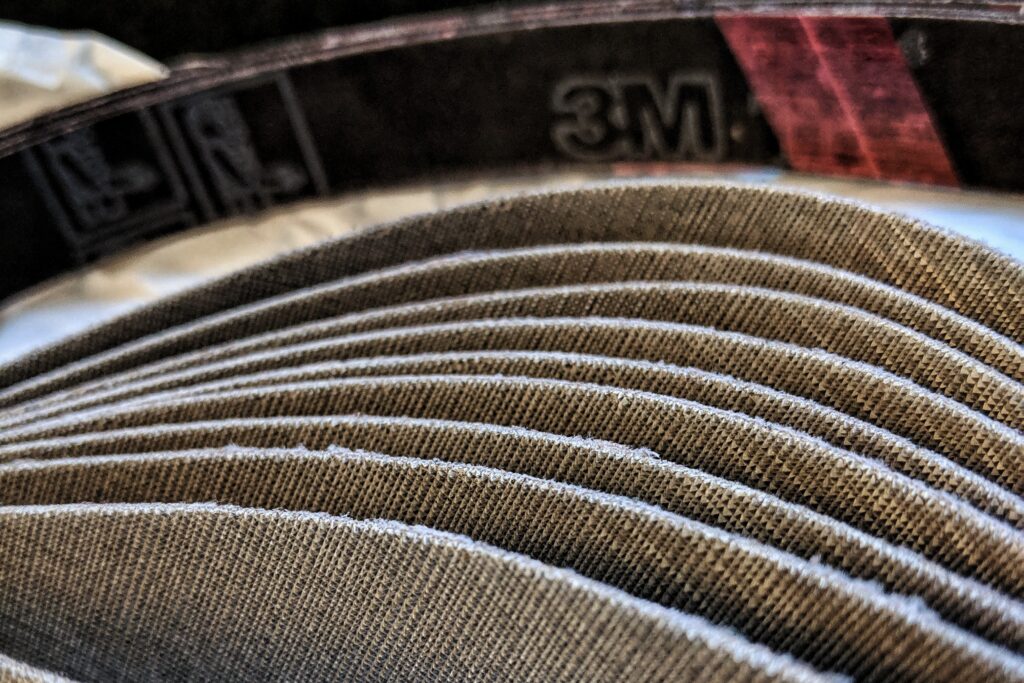
I did not have too good experiences with the belts on my grinder, they lost power too fast, but I had heard a lot about Trizact(TM) belts by 3M and I found a dealer who sells a pack of 10 in the needed length of 762 mm. And oh boy these belts are a game changer. I had ground in the bevels so much faster.
I was so eager to try out the new belts when they arrived, that I completely forgot to smoothen the edges/sides of the blade. That lead to some problems afterwards as it was a bit harder to get a good smooth line at the edge. I strongly recommend these Trizact belts (and i am not paid for it, this is just my personal opinion).
As my new forge (out of an old water tank) was not ready yet I had to do the whole heat treatment in my aerated concrete forge but that worked fine. I was not sure if the hardening worked until the whole knife was nearly finished and I tried to change a detail with a file – yes that blade is hard. I had no chance with the file.
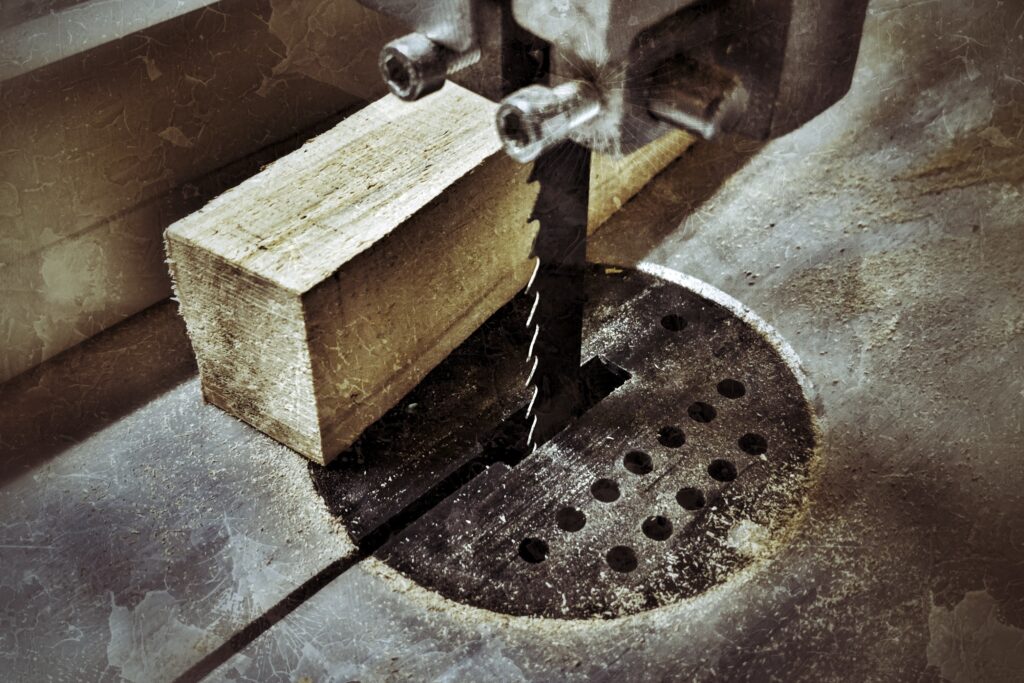
Next was the handle. The perfect chance to try out my new band saw. I had earned some extra money and that was perfectly spent for an Einhell TC-SB 305 U (again I am not paid for this). The bandsaw did a good job to cut a straight block out of a branch of our old apple tree. The first piece was too small in the end so I did a second one.
Next was the design of the guard, which I made out of steel I had bought at the local tool shop. I have no idea which kind of steel that is. Shaping that thing was easy, despite the fact that it felt harder than my knife steel when I tried to use my file on it. It got more complicated when I had to do the rectangular hole where the guard would sit on the blade.
This was when I realized that the thickness of the steel has a direct effect on how you can make the hole. I only had mini files to widen the narrow hole so the guard would sit perfectly on the blade. Fortunately I have a mini drill and that made things a lot easier when I needed to connect the holes I drilled into the guard. But in the future I wil use thicker steel so that I can use my larger files.
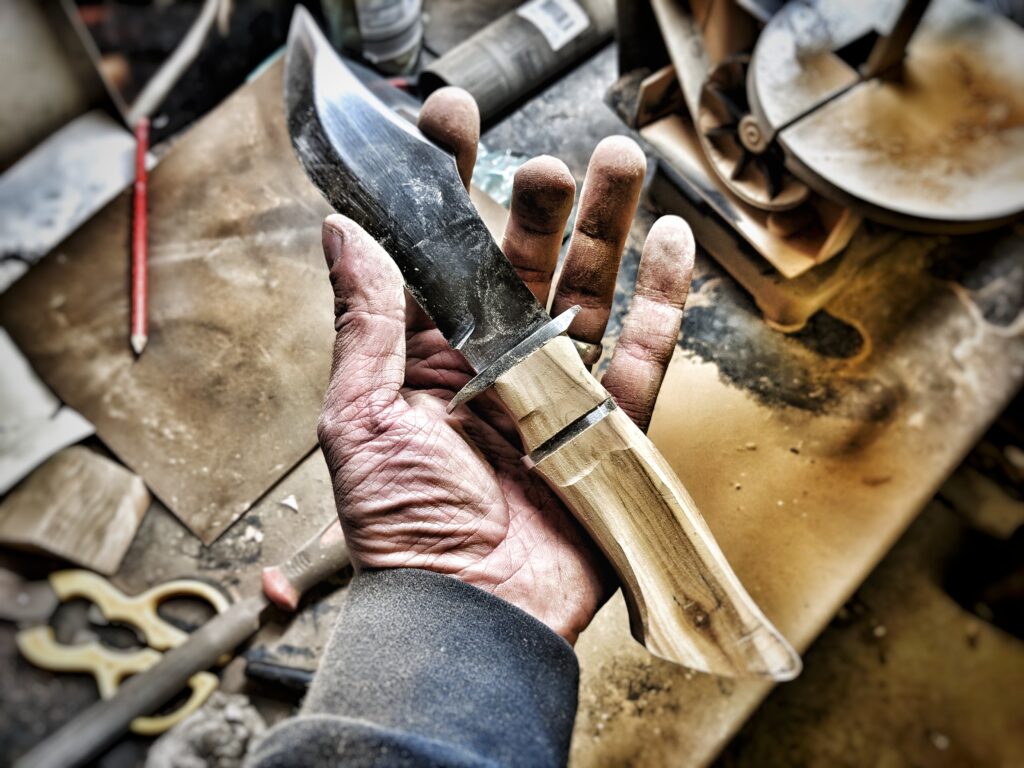
The same happened when it came to drilling out the wood of the handle. Additionally I had no drill bit that would be long enough for the whole tang. I did not want to shorten the tang as I was afraid to loose durability of the knife. So why not use it as an advantage – I had seen handle designs where there was a secondary steel part between index and middle finger which looked awesome. And so I would have the chance to make a deeper hole in the second part of the wood.
For widening the hole I needed something like a thin saw or file. Using a metal file would take too long. So I ended up bulding myself a hidden tang handle saw. I will blog about this in an extra post as this post is getting a bit long.
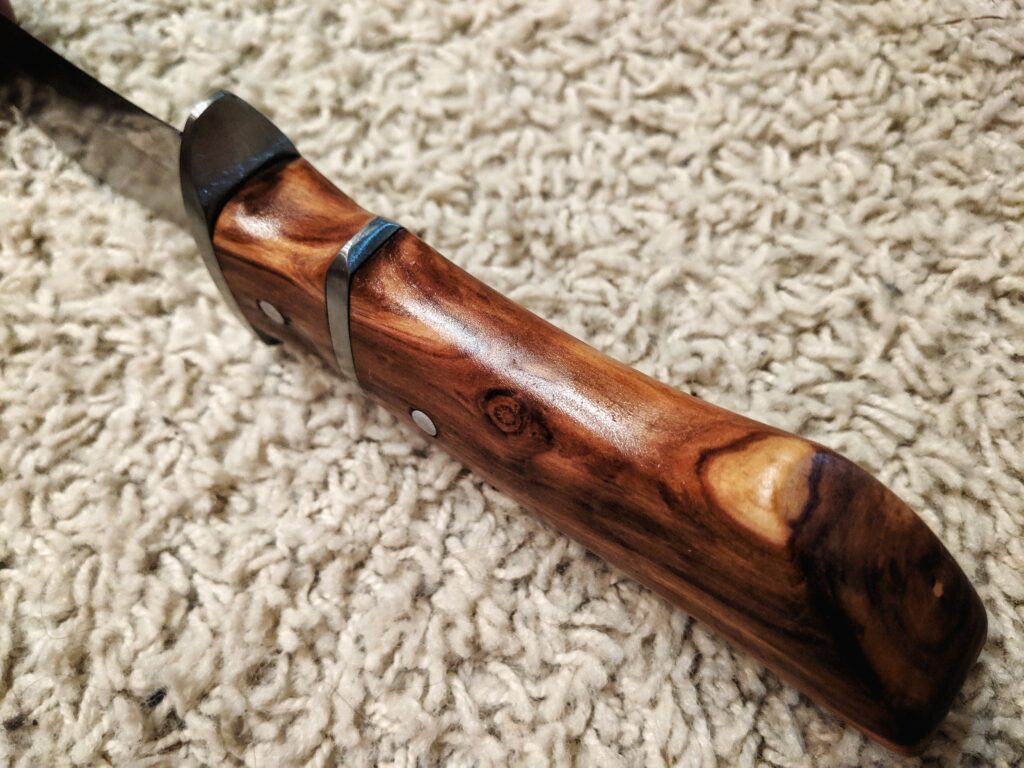
Finally I glued the parts to the tang with epoxy and ground the handle into shape. A good old friend of mine gave me the tip to polish the wood using steel wool – so that was a first time on this knife, too.